Bay Area Fulfillment for Fragile Electronics: A Guide for High-Tech Retailers
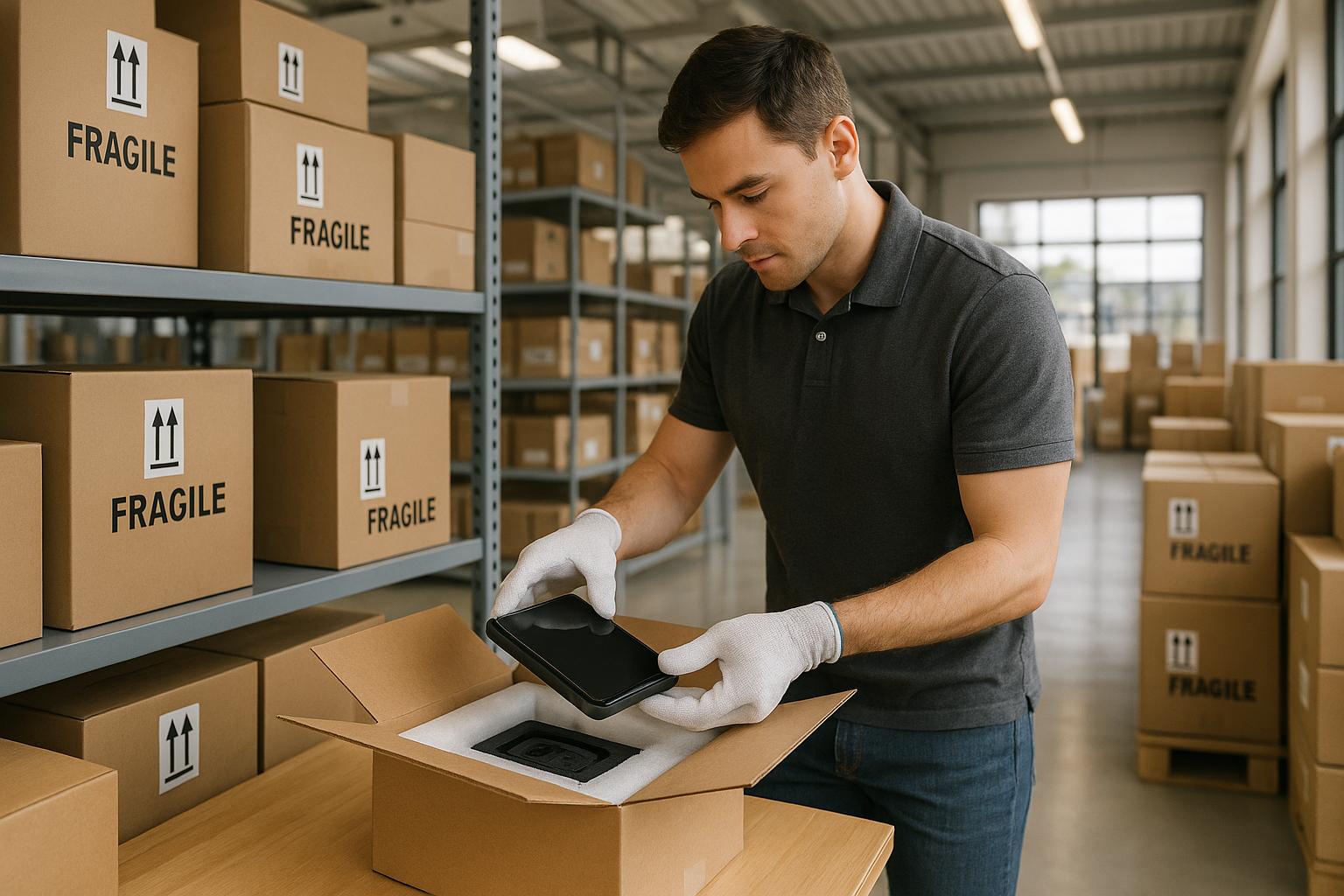
High-tech retailers face unique challenges when shipping fragile electronics like smartphones, tablets, and precision instruments. Damages during transit, customer dissatisfaction, and compliance with strict regulations make traditional shipping methods insufficient. To succeed, you need specialized fulfillment solutions that address:
- Risk Factors: Fluctuating temperatures, humidity, shocks, and vibrations can damage electronics.
- Packaging Needs: Custom foam inserts, anti-static materials, and double-boxing offer better protection.
- Staff Training: Proper handling techniques and regular audits ensure safe transit.
- 3PL Services: Third-party logistics providers with climate-controlled warehouses and advanced tracking systems can improve outcomes.
- White Glove Delivery: Premium services include careful handling, setup, and secure returns.
- Technology Integration: Tools like WMS, ERP, and RFID improve inventory accuracy and reduce errors.
For Bay Area retailers, partnering with a fulfillment provider that specializes in fragile electronics can reduce losses, improve customer satisfaction, and ensure compliance with industry standards.
Ultimate Guide to Packing and Shipping Electronics
Main Challenges of Fragile Electronics Fulfillment
Shipping fragile electronics comes with a unique set of hurdles that can make or break a retailer's success. Recognizing these challenges highlights why standard shipping practices often fall short when it comes to handling high-tech products.
How High-Tech Products Get Damaged
Electronic devices face a variety of risks during transit, many of which stem from environmental factors. For instance, fluctuating temperatures can cause serious issues like thermal stress, accelerated aging, and voltage drops. On the flip side, extremely low temperatures might lead to condensation and mechanical fatigue.
Humidity is another key factor. High humidity can allow moisture to seep into electronic components, resulting in corrosion and even short-circuiting. Meanwhile, low humidity increases the likelihood of electrostatic discharge (ESD), which can instantly destroy delicate circuits. Additionally, high humidity combined with surface contaminants can increase electrical conductivity, leading to signal interference or short circuits.
Physical damage is a constant concern as well. Rough handling during shipping is more common than you might think - around 10% of packages are damaged in transit, equating to roughly 1.5 billion parcels annually across all carriers. Fragile electronics are particularly vulnerable to damage caused by shocks, vibrations, temperature swings, and static discharge. These risks make precise handling and shipping measures an absolute necessity.
Shipping and Handling Requirements
To address these risks, fulfillment processes must include specialized controls and packaging solutions. Strict temperature and humidity management is crucial, often requiring tools like ventilation systems, cooling mechanisms, and insulation.
Proper training for staff is equally important. Employees must be well-versed in handling techniques, use the correct equipment for different types of electronics, and adhere to safety protocols. Regular audits help ensure these standards are consistently met.
When it comes to packaging, standard materials won’t cut it. High-quality packing supplies like sturdy boxes, bubble wrap, and foam inserts are essential. Packages should also be clearly marked with labels such as "Fragile", "Handle with Care", or "This Side Up." For items that are unusually shaped or particularly valuable, custom-designed packaging may be required. These measures help prevent damage from mishandling, insufficient cushioning, or improper labeling during transit.
Complying with DOT regulations is another critical step, especially for electronics containing batteries or other components classified as hazardous materials.
Condition monitoring technology provides a layer of reassurance by offering real-time data on factors like moisture, temperature, shocks, and location throughout the shipping process. This not only helps identify potential problems early but also provides documentation for insurance claims if damage occurs.
The financial stakes are high. Damage to fragile electronics doesn’t just mean replacing products; it also includes return shipping costs, customer service expenses, and the potential loss of customer trust. Fulfillment expert Will Schneider advises:
"Document the damage with photos, contact the seller immediately, and file a claim with the shipping carrier if needed."
Ultimately, prevention is far more cost-effective than dealing with the fallout of damaged goods. Proper handling, packaging, and monitoring are non-negotiable for fragile electronics.
These challenges highlight why fulfilling fragile electronics requires specialized solutions that go beyond standard shipping practices. In the upcoming sections, we’ll dive into specific strategies and technologies designed to meet these demands.
Safe Handling and Packaging Methods
To tackle packaging and handling challenges effectively, it's essential to combine protective materials with skilled staff. This approach minimizes damage during transit while ensuring customer satisfaction.
Protective Packaging Options
Good packaging does more than just look neat - it actively prevents damage. Custom foam inserts are a great example of this. These inserts are tailored to fit each product, creating a snug cradle that keeps items secure during shipping. They also absorb shocks and vibrations, reducing the risk of damage.
For electronics sensitive to electrostatic discharge (ESD), anti-static bags or foam are a must. Pairing these materials with desiccant packs can protect circuits from moisture, which helps prevent corrosion and short-circuiting in humid conditions.
Another effective method is double-boxing, especially for high-value or fragile items. This involves placing the product in a smaller, cushioned box, which is then placed inside a larger box with additional padding. The inner box absorbs initial impacts, while the outer box provides an extra layer of protection, making this method particularly reliable.
When packing individual items, wrap each piece in bubble wrap or foam sheets, ensuring the material directly touches the product. Fill any gaps with packing materials to prevent movement and add extra padding to handle stacking pressure. For fragile items, use partitions to give each piece its own space and reduce the chance of items bumping into each other. To protect against moisture, consider waterproof materials or seal products in plastic bags before placing them in the outer box.
Finally, secure all packages with extra padding and seal them tightly. Clear labeling with instructions like "Fragile", "Handle with Care", or "This Side Up" ensures handlers treat shipments appropriately.
-
Packaging Material
-
Custom Foam Inserts
- Best Use Case: High-value electronics, irregular shapes
- Protection Level: Highest shock absorption
-
Anti-Static Bags/Foam
- Best Use Case: Circuit boards, sensitive components
- Protection Level: ESD protection
-
Double-Boxing
- Best Use Case: Valuable items, long-distance shipping
- Protection Level: Maximum overall protection
-
Corrugated Dividers
- Best Use Case: Multiple items in one box
- Protection Level: Good separation and cushioning
-
Custom Foam Inserts
Training Staff to Handle Electronics
Even the most secure packaging won't matter if items are mishandled. That's where staff training comes in. Employees need to understand the specific risks associated with different types of electronics. For instance, handling a smartphone requires a different approach than managing larger items like monitors or server equipment.
Hands-on practice sessions can help staff master proper grip, lifting techniques, and positioning for various products. Training should also cover the use of tools like dollies, hand trucks, and other mechanical aids. Knowing when to rely on these tools versus manual handling - and how to secure items during in-warehouse transport - is key to reducing drops and damage.
To maintain high standards, companies should provide regular refresher courses. Periodic audits using detailed checklists can ensure staff consistently follow safe handling protocols. Visual guides and documented procedures can further emphasize why proper handling is crucial - not just for avoiding damage, but also for improving customer satisfaction and reducing costs.
3PL Services for Fragile Electronics
Third-party logistics (3PL) providers specialize in tackling the challenges of handling fragile electronics. These services cover everything from secure storage and careful transportation to professional delivery, ensuring the safety of sensitive items every step of the way.
Many 3PL providers use warehouses equipped with climate control and ESD-safe (Electrostatic Discharge) measures. These facilities are designed to maintain ideal temperature and humidity levels while employing anti-static storage solutions to protect delicate components from damage.
A full-service 3PL solution typically includes secure storage, custom packaging designed for sensitive electronics, expert handling protocols, insured shipping, and efficient returns management. On top of that, modern 3PL providers offer real-time tracking across inventory and sales channels. This means retailers can monitor their products from the moment they leave the warehouse until they reach the customer. Next, we’ll explore premium delivery options and how returns processes are optimized for fragile electronics.
White Glove Services for Delicate Items
White glove services provide an elevated level of care for high-value electronics, ensuring not just the safety of the product but also a premium customer experience. This service goes far beyond standard delivery, offering a complete process that includes inside delivery to a specific room, professional unpacking, assembly or setup of the product, and removal of packaging materials. The goal is to deliver the item in a ready-to-use state.
Packaging for white glove services is specifically designed to match the product’s weight and protection needs, including shock absorption and environmental safeguards. Enhanced security measures - like real-time tracking, secure storage, and strict background checks for personnel - add an extra layer of protection for these valuable items. The cost for white glove services typically ranges between $100 and $250 per shipment, with additional fees for more complex installation or assembly tasks. Insurance coverage is generally included to further protect the shipment.
White glove delivery is often paired with streamlined returns processes, which help manage any issues with minimal hassle for both the retailer and the customer.
Returns Management (RMA) Processes
Handling returns for fragile electronics demands a specialized approach. 3PL providers manage every step, including diagnostics, restocking, refurbishing, and eco-friendly recycling. During diagnostics, trained technicians determine whether returned products are defective, damaged during shipping, or simply unwanted. Based on this assessment, items are either restocked, refurbished, or processed as defective.
To prevent additional damage during the returns process, these providers rely on secured facilities and careful handling. Efficient returns management not only resolves customer issues quickly but also helps recover product value. Compliance with industry regulations - such as safe handling of lithium-ion batteries and proper electronic waste disposal - is a critical part of the process. Integration with inventory systems ensures real-time visibility into returned items, enabling better decisions about restocking, refurbishing, or disposal.
sbb-itb-eafa320
Using Technology for Better Fulfillment
When it comes to protecting fragile electronics during fulfillment, advanced technology is a game-changer. Modern systems help reduce mistakes, provide real-time tracking, and automate warehouse tasks - ensuring these delicate items are handled with precision.
Warehouse Management Systems (WMS)
A Warehouse Management System (WMS) simplifies every step of warehouse operations, from receiving inventory to shipping orders. It provides real-time updates on stock levels, automates repetitive tasks, and optimizes space and labor allocation. This level of efficiency is crucial for handling high-value electronics. For example, studies reveal that order picking alone can account for 55% of total warehousing costs. By streamlining workflows, a WMS not only reduces errors but also enhances productivity. Pairing a WMS with an ERP system can take this efficiency even further by centralizing data and processes.
Integration with ERP Systems
Integrating ERP systems allows businesses to connect inventory, logistics, and customer data in one place. This integration reduces manual errors and provides the detailed financial visibility required for managing fragile electronics. Take Touchland LLC, for instance - they used NetSuite ERP to scale operations across thousands of locations, showcasing how integration can drive efficiency. The global retail ERP market is expected to grow from $10.34 billion in 2023 to $28.58 billion by 2032, reflecting the increasing demand for these systems. Such tools also help prevent customer churn, which is critical given that 32% of consumers may abandon a brand after a single poor experience. Alongside ERP systems, technologies like barcode and RFID tracking ensure every electronic item is accounted for at every stage of the supply chain.
Barcode and RFID Systems
Barcode and RFID technologies provide the detailed tracking needed to manage fragile electronics effectively. Barcodes are cost-efficient, with labels priced at just a few cents each, but they require direct line-of-sight scanning. RFID tags, on the other hand, store more data and can be read simultaneously, achieving inventory accuracy rates as high as 99.9% while reducing handling errors. One retailer, for example, saw a 16% drop in out-of-stock instances and boosted sales by over $100 million after adopting RFID. Additional benefits include cutting search times for misplaced items by 80% and reducing order processing times from 48 hours to just 12.
Although RFID tags cost between $1 and $30 each, with readers priced accordingly, their added security features - like encryption and authentication - make them ideal for high-value electronics. Major companies like Walmart, Zara, and Delta Air Lines have successfully implemented RFID systems, with UHF RFID tags becoming a favorite due to their long reading range and fast data transmission. Emerging technologies like blockchain are also being explored to further enhance record security.
Choosing a Bay Area Fulfillment Partner
When it comes to fragile electronics, picking the right fulfillment partner can make all the difference. The Bay Area's competitive market demands providers who go beyond basic warehousing, offering specialized services tailored to delicate, high-tech products. Knowing what to prioritize can help you zero in on the ideal partner.
What to Look for in 3PL Partners
Location and Regional Coverage
For Bay Area retailers, a fulfillment partner with warehouses in key California markets - like San Francisco, Los Angeles, and San Diego - is a must. This ensures quicker deliveries and better access to local markets. Faster shipping times are especially critical for fragile electronics, where customer satisfaction hinges on timely and safe delivery [50, 51].
Industry Experience and Specialization
Experience matters. Look for providers who have a proven track record with fragile electronics. Ask for references from other electronics retailers to confirm their expertise and reliability [2, 12, 53].
Technology Integration
Your 3PL should have an advanced Warehouse Management System (WMS) that integrates seamlessly with your existing systems. Features like real-time dashboards and tracking tools can help you monitor key metrics, reduce breakage rates, and improve customer satisfaction [50, 55].
Flexibility and Customization
Scalability is essential when handling fragile electronics. Choose a 3PL that can adapt to your needs, whether it’s scaling up during peak seasons or customizing services to fit your growth plans. This ensures you’re prepared for future demand without sacrificing quality [2, 50].
Specialized Services
A strong fulfillment partner will offer services specifically designed for fragile items. These might include custom packaging solutions (like foam or bubble wrap), trained staff familiar with handling delicate goods, and established relationships with reliable carriers across California. Efficient tracking and delivery confirmation processes are also key [51, 53, 55].
It’s worth noting that 93% of customers are more likely to return after a positive service experience. This underscores the importance of partnering with a provider that prioritizes careful handling and dependable delivery.
Comparison Table for Evaluating Fulfillment Partners
To simplify your decision, here’s a quick comparison table highlighting key criteria, questions to ask, and red flags to watch for:
-
Evaluation Criteria
-
Location & Coverage
- Requirements: Bay Area presence, strategic warehouse locations
- Questions to Ask: Do you have warehouses in SF, LA, and San Diego? What’s your average delivery time to major CA markets?
- Red Flags: Limited regional coverage, no local presence
-
Electronics Experience
- Requirements: Proven expertise with fragile items, client references
- Questions to Ask: Can you provide references from electronics retailers? What’s your breakage rate for fragile items?
- Red Flags: No electronics experience, high damage rates
-
Technology Integration
- Requirements: Advanced WMS, real-time tracking, inventory visibility
- Questions to Ask: Does your WMS integrate with our systems? What reporting capabilities do you offer?
- Red Flags: Outdated systems, no integration options
-
Specialized Services
- Requirements: Custom packaging, white glove handling, climate control
- Questions to Ask: What packaging materials do you use for electronics? How do you handle returns?
- Red Flags: Generic packaging only, no specialized services
-
Scalability & Flexibility
- Requirements: Seasonal capacity, service customization
- Questions to Ask: Can you handle peak season volumes? What’s your capacity expansion timeline?
- Red Flags: Rigid contracts, no scalability options
-
Cost Structure
- Requirements: Transparent pricing, no hidden fees
- Questions to Ask: What are your storage, pick/pack, and shipping rates? Are there any hidden fees?
- Red Flags: Unclear pricing, excessive additional charges
-
Location & Coverage
One standout example is AP Express Logistics. With over 33 years of experience, their 2.1 million square feet of warehouse space across Los Angeles, Corona, and Las Vegas, combined with a fleet of 74 owned trucks, ensures seamless warehousing, distribution, and last-mile delivery solutions.
Clear communication about your products’ dimensions, weight, and fragility is crucial to ensure proper handling throughout the fulfillment process. Be mindful of balancing the scale of large 3PLs with their responsiveness - some may be slower to adapt or come with higher costs.
JIT Transportation: Scalable Fulfillment Solutions for Fragile Electronics
For over 30 years, JIT Transportation has built a strong reputation for tackling the complex fulfillment needs of high-tech retailers. Their expertise in handling fragile electronics extends well beyond basic warehousing, offering comprehensive solutions tailored to high-value, delicate products. This specialized approach forms the backbone of their 3PL services.
Custom 3PL Solutions for High-Tech Retailers
JIT Transportation doesn’t just stop at standard logistics. Their White Glove Services are specifically designed to handle high-value, fragile, and time-sensitive shipments, ensuring premium care and security every step of the way.
"Yes, we specialize in high-value, fragile, and time-sensitive shipments with our White Glove Services, ensuring premium handling and security." - JIT Transportation
Beyond their White Glove offerings, JIT provides a range of solutions to meet the unique needs of electronics retailers. Their specialized pick-and-pack operations are tailored to handle delicate components with care. For businesses managing complex products, JIT’s kitting and assembly services combine multiple components into ready-to-ship packages, reducing handling and minimizing the risk of damage.
JIT also offers testing and firmware or software updates at the warehouse level, ensuring products are fully functional before they’re shipped. This added step means customers receive electronics in perfect working order. To further protect fragile items, JIT collaborates with clients to create custom packaging solutions that meet the specific needs of products like smartphones, tablets, or even sensitive medical devices.
Bay Area Warehousing and Nationwide Reach
With 14 strategically located warehouses across the U.S., JIT Transportation offers over 2.5 million square feet of warehousing space. This network allows Bay Area retailers to position inventory closer to major markets while maintaining the specialized handling required for fragile electronics.
JIT’s commitment to punctuality is evident in their impressive 98.5% on-time rate for regional LTL shipments. Timeliness is critical for fragile electronics, where delays can lead to damage or unhappy customers. By operating a dedicated fleet, JIT minimizes reliance on third-party carriers, further enhancing reliability. Their final-mile delivery services include protocols like signature confirmation and precise placement, ensuring safe and secure arrivals.
Technology Solutions and System Integration
JIT Transportation leverages advanced technology to streamline logistics. Their Warehouse Management System (WMS) provides real-time visibility into inventory and shipments, while API integrations allow seamless connectivity with e-commerce platforms and ERP systems. This automation reduces manual errors and keeps operations running smoothly.
"We provide custom logistics solutions, including distribution, fulfillment, transportation, and value-added services. We specialize in scalable, flexible, and technology-driven logistics to optimize supply chains for businesses of all sizes." - JIT Transportation
Real-time tracking systems offer detailed oversight at every stage, from inventory receipt to delivery, enabling proactive issue resolution. Their scalable eCommerce fulfillment platform grows with businesses, eliminating the need for costly system overhauls.
JIT prioritizes safety across all operations, reducing cargo damage and enhancing security measures - essential for handling fragile electronics.
"At JIT, safety is everyone's responsibility, and we take it very seriously. It is the foundation of our success and our commitment to it applies to all employees, from executive management to the newest hire." - JIT Logistics
Conclusion: Getting Reliable Fulfillment for Fragile Electronics
Handling fragile electronics goes far beyond standard warehousing and shipping. High-tech retailers in the Bay Area need partners who truly understand the complexities involved - everything from protective packaging to precise handling protocols. The stakes couldn’t be higher. A single damaged shipment can lead to lost revenue, dissatisfied customers, and even harm to a brand’s reputation. That’s where JIT Transportation steps in. With over 30 years of experience, they’ve mastered the art of delivering the precision and care that fragile electronics demand. Their strategy blends expert handling, advanced technology, and strategic warehouse locations, including facilities in San Francisco and Sacramento. This combination ensures they can meet growing demands with ease.
JIT has built a reputation for scaling operations while maintaining the meticulous care that delicate products require. Their extensive warehousing capabilities and broad carrier network allow them to handle everything from the modest needs of startups to the complex demands of enterprise-level operations. Whether it’s managing seasonal surges or launching new products, JIT’s infrastructure grows alongside your business - without ever compromising on quality.
Their reliability speaks for itself, especially in their partnerships with major technology companies. Hal Shapiro of Seagate Technology highlights this consistency:
"JIT has been a trusted logistics partner for Seagate for years, and their reliability is unmatched. Day in and day out, they prove their commitment to seamless operations, ensuring our supply chain stays on track. We know we can count on JIT to deliver, every time."
This level of trust and proven success underscores the importance of choosing a specialized fulfillment partner. In an industry where every mishandled shipment can ripple through revenue and reputation, having a reliable logistics partner is critical.
For high-tech retailers, the right fulfillment partner safeguards products, keeps customers happy, and supports business growth. JIT Transportation’s blend of specialized expertise, cutting-edge technology, and decades of experience makes them uniquely equipped to handle the intricate demands of fragile electronics fulfillment in the Bay Area and beyond.
FAQs
What should high-tech retailers look for in a fulfillment partner for fragile electronics in the Bay Area?
When choosing a fulfillment partner for fragile electronics, it's crucial to focus on their experience with handling delicate items and their ability to offer customized packaging solutions that safeguard your products during transit. Partnering with a provider near your Bay Area customers can also lead to quicker deliveries and happier customers.
It's equally important to select a provider with strong inventory management systems and advanced tracking tools to keep the shipping process clear and reliable. A history of safely managing fragile electronics is a clear sign that they can deliver your products intact and on schedule.
How do logistics providers ensure the safe delivery of fragile electronics?
Logistics providers have developed tailored approaches to ensure fragile electronics are transported safely and securely. They rely on trained personnel who are well-versed in the specific needs of high-tech products, use shock-resistant packaging to guard against potential impacts, and employ real-time monitoring systems to keep an eye on conditions like temperature and humidity throughout the journey.
On top of that, they collaborate with carriers skilled in handling delicate items and enforce strict quality checks at every step. These efforts work together to ensure your high-tech products reach their destination intact and in excellent condition.
What key technologies help ensure safe and efficient shipping of fragile electronics?
When it comes to shipping fragile electronics, using the right technology is key to keeping them safe and ensuring smooth delivery. Tools for real-time monitoring, such as GPS, RFID, and impact sensors, are incredibly useful. They track the package's condition and can detect any strong impacts or mishandling during transit, reducing the chance of damage.
On top of that, AI-driven route planning and predictive analytics make deliveries more efficient. By identifying the safest and most reliable routes, these systems help protect delicate items while also improving accuracy. Together, these technologies work to make sure your fragile electronics reach their destination in excellent shape.
Related posts
Related Articles

How 3PLs Support Green Reverse Logistics
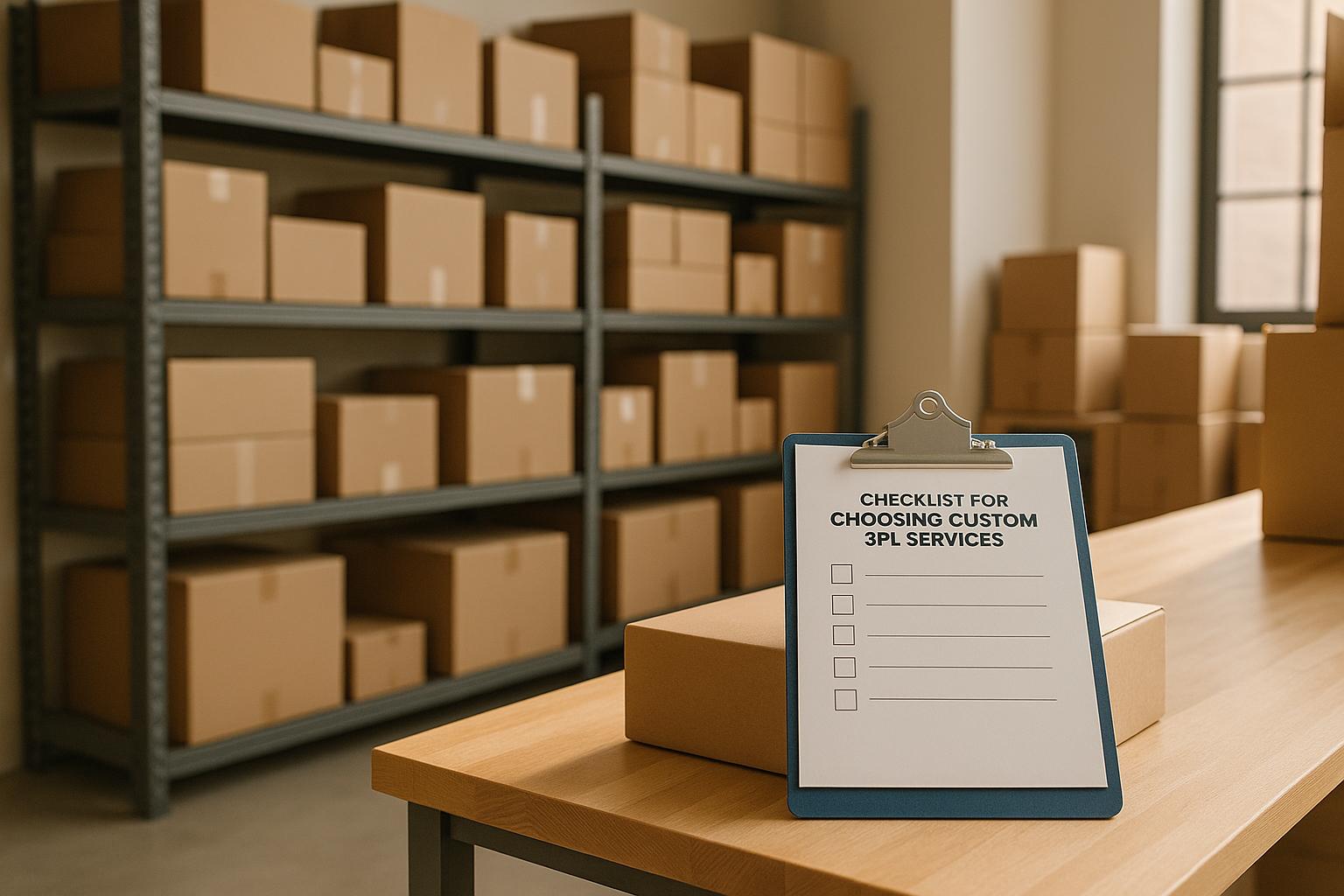
Checklist for Choosing Custom 3PL Services
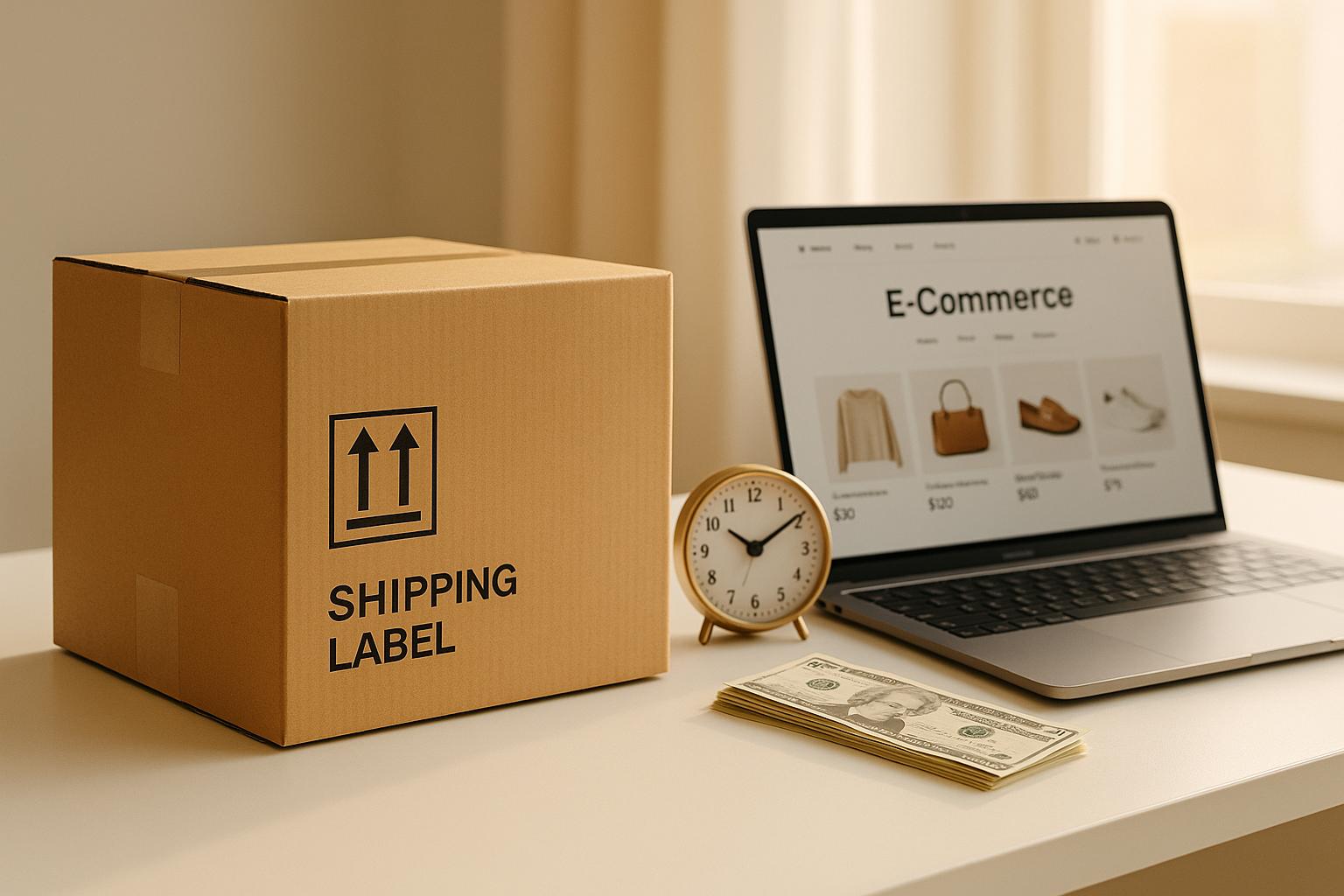