Fragile Electronics Fulfillment in the Bay Area vs. Reno: Which Is Better for Your Brand?
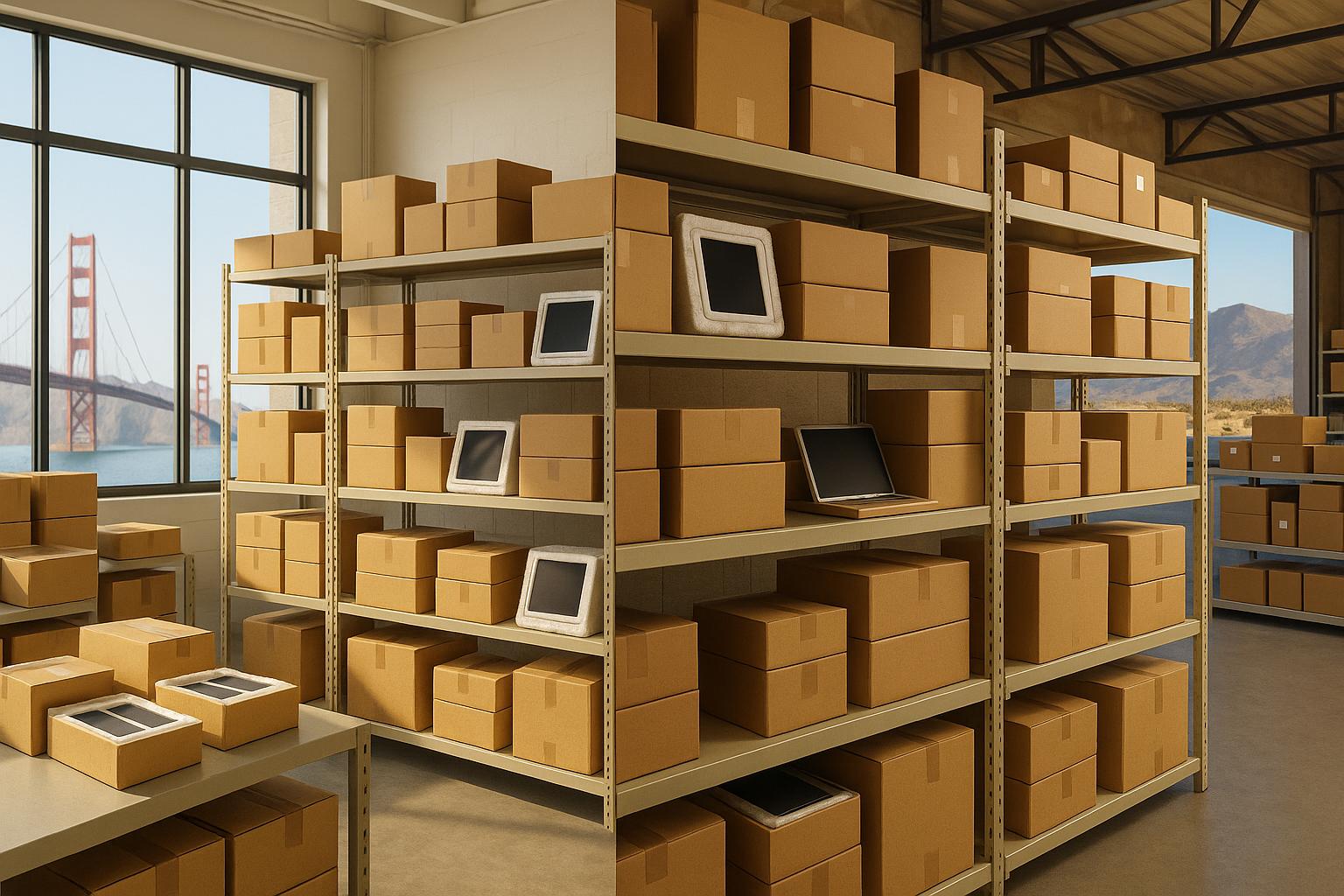
For fragile electronics fulfillment, the choice between the Bay Area and Reno depends on your priorities: cost savings or proximity to tech hubs.
- Bay Area: Offers access to Silicon Valley, advanced logistics, and faster delivery to major markets. However, it comes with high costs for labor, warehousing, and transportation.
- Reno: Provides lower operational costs, tax advantages, and efficient access to Western markets via the I-80 corridor. While less expensive, it may lack the infrastructure density of the Bay Area.
Quick Comparison
-
Factor
-
Bay Area
- Operating Costs: High
- Market Access: Close to Silicon Valley
- Fulfillment Speed: Faster local delivery
- Tax Policies: Higher taxes
- Infrastructure: Advanced logistics
-
Reno
- Operating Costs: Lower
- Market Access: Strategic Western location
- Fulfillment Speed: Slightly longer transit
- Tax Policies: No inventory or corporate taxes
- Infrastructure: Growing network
-
Bay Area
Choose the Bay Area for premium logistics and speed or Reno for affordability and scalability.
3PL Models: Finding the Right Fit for Every Growth Stage 📦 #3PL #SupplyChain #LogisticsSolutions
Bay Area: Fulfillment Benefits and Drawbacks
The Bay Area is a prime location for electronics fulfillment, offering unmatched access to key markets but also bringing significant operating expenses. These factors directly impact the safe and efficient delivery of delicate electronics.
Close Access to Major Markets
The Bay Area's proximity to Silicon Valley and other Northern California markets provides a critical advantage for fulfilling high-value electronics orders. Being close to these hubs ensures quicker last-mile delivery, which is essential for time-sensitive shipments. Additionally, the nearby Port of Oakland offers direct access to international supply chains, making it easier to manage inventory from overseas manufacturers. The region's tech-driven economy also means a skilled workforce familiar with handling fragile electronic products is readily available. However, these benefits come with a hefty price tag.
High Operating Costs
Operating in the Bay Area means grappling with some of the highest costs in the country. Real estate prices are steep, with warehouse space averaging $9.47 per square foot by 2025, accompanied by rising minimum monthly rates. Labor costs are another major factor, with San Francisco's minimum wage set at $15.59 per hour, warehouse staff earning an average of $17.14 per hour, and management salaries around $53,102 annually. On top of that, utilities cost at least $2 per square foot annually, and strict regulations could push energy costs even higher.
Transportation costs further compound the issue. Traffic congestion and limited parking in San Francisco make logistics more expensive, increasing the cost of moving products in and out of fulfillment centers. While these challenges drive up expenses, the Bay Area's advanced fulfillment capabilities help offset some of the financial strain.
Advanced Infrastructure and Services
Despite the high costs, the Bay Area boasts cutting-edge fulfillment services tailored to the unique needs of fragile electronics. The region is home to numerous third-party logistics (3PL) providers specializing in tech and electronics, offering services like precise pick-and-pack operations and thorough quality control. Many fulfillment centers in the area also feature advanced warehouse management systems, real-time inventory tracking, and seamless e-commerce integration. These tools ensure that delicate electronics are handled and shipped with care and accuracy.
The region's focus on technology and process improvements supports top-tier electronics fulfillment. Businesses can navigate the high costs by adopting strategies like automation to reduce labor expenses, negotiating better shipping rates, and exploring renewable energy options to control utility spending. Partnering with experienced 3PL providers is essential to leveraging the Bay Area's strengths while managing its cost challenges effectively.
Reno: Fulfillment Benefits and Drawbacks
Reno presents a compelling option for fragile electronics fulfillment, offering cost savings, a prime location in the Western U.S., and an appealing tax landscape. Let’s explore these advantages in more detail.
Lower Costs and Growth Potential
Reno is a cost-efficient alternative to other major hubs like San Francisco. The overall cost of living in Reno is 65.3% lower than in San Francisco, making it an attractive choice for businesses looking to reduce expenses. For example, warehouse and office lease rates in Reno range from $0.38 to $0.48 per square foot, compared to $0.55 to $0.85 in California. Premium office spaces show an even greater disparity, with Class A office leases costing $30 to $39 per square foot in Reno versus $78 to $84 in San Francisco.
Labor costs are another area where Reno shines. With wages in Nevada averaging about 33% less than in California, businesses can offer competitive pay while keeping expenses in check. Workers' compensation rates are also lower, adding just $1.18 per $100 in wages in Reno versus $2.87 in the Bay Area.
Utility rates in Reno further enhance its cost advantages. Businesses in Reno pay about $0.078 per kilowatt hour for electricity, while those in San Francisco pay nearly double at $0.157. For companies operating climate-controlled facilities or using energy-intensive equipment, these savings can lead to substantial monthly reductions. Combined, these lower costs create a strong foundation for business growth.
"Reno is exploding from an industrial standpoint." - Tom Theobald, Mohr Capital
Central Western US Location
Reno’s location is another major asset. Situated in the heart of the Western U.S., it provides efficient access to key markets without the traffic and logistical headaches often associated with coastal cities. Reno’s natural positioning as a distribution hub allows businesses to optimize shipping routes, reduce transit times, and serve a broad customer base more effectively.
Additionally, the industrial zones around Reno are less congested, enabling more predictable shipping schedules and lower transportation costs. Businesses can further streamline their operations by using routing software and GPS tracking to avoid delays and minimize travel distances. This level of efficiency makes Reno an ideal choice for companies focused on logistics and fulfillment.
Business-Friendly Tax Environment
Nevada’s tax policies offer significant advantages. The state imposes no corporate, inventory, franchise, personal, inheritance, estate, unitary, or intangibles taxes. In fact, Nevada ranked as the #3 most business-friendly tax climate in the U.S. according to a 2015 Tax Foundation Index.
For companies managing inventory, the absence of an inventory tax can lead to substantial savings. One business eliminated a $168,000 tax liability simply by relocating its inventory to Nevada. Beyond these tax benefits, Nevada offers additional incentives, such as workforce development programs through the Silver State Works Program. As a right-to-work state, Nevada also provides businesses with more operational flexibility.
"The Reno-Sparks area is special when it comes to logistics and distribution. We are essentially the center of the West from a distribution and e-commerce perspective, with not only a superb business climate but a wonderful place to live as well." - Mike Kazmierski, CEO of EDAWN
sbb-itb-eafa320
3PL Solutions for Fragile Electronics
Navigating regional cost variations and infrastructure challenges makes advanced 3PL services essential for handling delicate electronics. Partnering with a specialized 3PL provider ensures the careful handling, quality control, and seamless integration of technology needed for items like smartphones, tablets, and high-end audio equipment.
Handling and Quality Control
JIT Transportation offers white glove services, combining premium packaging with precise transportation protocols to protect high-value electronics throughout the fulfillment process. This meticulous approach ensures that fragile products, such as high-end audio systems, are handled with the utmost care.
Once products arrive, thorough inspections - including counting, documenting, and photographing any damages - help establish accountability. Additional services like kitting, assembly, testing, revision upgrades, custom labeling, and specialized handling further safeguard product integrity during fulfillment.
Industry benchmarks highlight the precision required in electronics logistics. Advanced tracking systems maintain inventory accuracy rates of 99.5% or higher, while precise picking processes ensure order accuracy rates of up to 99.9%.
Technology Integration
JIT Transportation's integrated Warehouse Management System (WMS) provides real-time inventory and shipment tracking. It automates order processing, seamlessly updates ERP systems, and integrates with popular e-commerce platforms like Shopify, Magento, and WooCommerce.
"Our advanced Warehouse Management System (WMS) offers real-time tracking and order accuracy tools. Combined with trained staff and quality control protocols, we ensure timely and precise fulfillment."
– JIT Transportation
Growth Support and Added Services
With over 1 million square feet of warehouse space across 14 locations and more than 30 years of experience, JIT Transportation is well-equipped to scale alongside your brand. Their expertise extends to streamlining reverse logistics with efficient returns management.
Their comprehensive services include pick and pack operations, vendor-managed inventory (VMI) programs, and pool distribution and consolidation services. These solutions help optimize stock levels and reduce shipping costs, offering brands the flexibility they need to grow.
Client feedback underscores the value of these services:
"JIT has been a trusted logistics partner for Seagate for years, and their reliability is unmatched. Day in and day out, they prove their commitment to seamless operations, ensuring our supply chain stays on track."
– Hal Shapiro, Seagate Technology
During peak seasons or product launches, scalability becomes even more critical. JIT Transportation's infrastructure is designed to adapt to fluctuating volumes. Their nationwide network, which includes over 500 carriers and more than 200 trucks, ensures consistent service levels regardless of demand.
These tailored 3PL solutions empower brands to select the ideal fulfillment hub for their fragile electronics, ensuring reliability and efficiency at every step.
Bay Area vs. Reno: Side-by-Side Comparison
Choosing between the Bay Area and Reno requires careful consideration of costs, market access, and service capabilities.
The Bay Area benefits from its proximity to major tech companies and well-established supply chains, but these advantages come at a steep price. High labor, warehousing, and real estate costs make operations expensive. Additionally, heavy traffic congestion increases delivery times and last-mile costs, especially for fragile electronics that need specialized handling.
Reno, on the other hand, offers a more cost-effective alternative. Lower expenses in labor, warehousing, and transportation make it an attractive option. Its location along the I-80 corridor provides convenient access to the Bay Area at a fraction of the cost. For example, transit from Oakland to Reno takes 13–22 days by sea and only 2–3 days by truck.
Air freight options also add flexibility. Shipments from Chinese airports can reach Reno-Tahoe or San Francisco in 3–7 days, with final trucking from SFO to Reno taking just 1–2 hours. This logistical agility is particularly useful for tech companies managing product launches or addressing supply chain disruptions.
Below is a side-by-side comparison of key metrics to help weigh the options:
Comparison Table: Key Metrics
-
Factor
-
Bay Area
- Operating Costs: High labor, warehousing, and real estate costs
- Market Proximity: Direct access to major tech companies and consumers
- Transit Times: Immediate local delivery; high congestion costs
- 3PL Service Availability: Higher concentration of specialized providers
- Growth Potential: Limited by high costs and space constraints
- Shipping Routes: Premium local access; expensive regional distribution
- Climate Considerations: Mild year-round conditions
-
Reno
- Operating Costs: Lower costs with potential for growth; reduced leasing rates
- Market Proximity: Strategic I-80 location with 1–2 hour access to Bay Area
- Transit Times: 13–22 days by sea + 2–3 days by truck from West Coast ports
- 3PL Service Availability: Expanding network offering cost-effective solutions
- Growth Potential: Expanding infrastructure and business-friendly environment
- Shipping Routes: Efficient and cost-effective regional shipping
- Climate Considerations: Variable temperatures with winter snow (Nov–Mar)
-
Bay Area
While the Bay Area boasts a higher concentration of specialized 3PL providers due to its established tech ecosystem, Reno is rapidly building its logistics infrastructure. Reno’s growing network offers cost-effective solutions that can help reduce fulfillment expenses without compromising service quality.
Weather is another factor to consider. The Bay Area enjoys mild, consistent conditions year-round, whereas Reno faces more variable weather, including winter snow in the Sierra Nevada region. To mitigate these challenges, logistics providers in Reno offer climate-controlled transport and flexible scheduling. It's generally advised to avoid peak winter months (November through March) for trucking through mountain passes.
Choosing the Right Location for Your Brand
Deciding between the Bay Area and Reno comes down to your priorities, budget, and long-term growth plans. Each location has its strengths, catering to different business needs and models.
If keeping costs low is a priority, Reno is a compelling choice. Operating expenses in Reno are much lower compared to the Bay Area, thanks to reduced electricity costs, affordable office spaces, and lower wages. On top of that, Nevada’s tax policies provide additional financial relief. The state imposes no corporate or personal income taxes, no inventory tax, and no franchise tax. Payroll payments are capped at $36,000 annually, unlike California, which has no such cap. As Tom Theobald of Mohr Capital puts it:
"Reno is exploding from an industrial standpoint".
These cost savings can create a strong financial base, especially when paired with Reno’s logistical and market advantages.
Market access is another significant consideration. Reno’s location along the I‑80 corridor allows one-day truck service to over 60 million customers and two-day service to 11 western states. The Reno-Tahoe International Airport also plays a major role, handling 139 million pounds of cargo in 2022, which enables next-day delivery to much of the West Coast. Additionally, Reno benefits from its designation as a port of entry and has direct rail connections to the Port of Oakland, making it a hub for efficient distribution.
For businesses dealing with specialized electronics or other delicate products, partnering with a 3PL experienced in handling sensitive goods is critical. Advanced capabilities like white glove handling, climate-controlled transportation, and regulatory compliance ensure products are protected throughout the supply chain. Companies like JIT Transportation even offer services such as testing, upgrades, and secure packaging to meet these high standards.
For brands focused on growth, Reno’s expanding logistics and transportation infrastructure, coupled with Nevada’s business-friendly legal and regulatory environment, provides a strong platform for scaling operations.
Ultimately, your choice should align with your financial goals, market access needs, and operational priorities. The Bay Area is ideal if proximity to major tech companies and established supply chains is crucial. On the other hand, Reno offers cost savings, tax advantages, and strategic access to western markets. Carefully weigh these factors to determine which location best supports your brand’s vision and strategy.
FAQs
What makes Reno a better choice than the Bay Area for fulfilling fragile electronics orders?
Reno is an attractive option for handling fragile electronics fulfillment, offering a balance of affordability and convenience. With lower costs for warehouse space and labor compared to the Bay Area, businesses can save considerably on operational expenses. Plus, Reno's location close to major West Coast markets means quicker delivery times, which is a huge win for meeting customer expectations.
The city also boasts access to specialized third-party logistics (3PL) providers experienced in managing delicate products. This ensures your fragile electronics are handled with the care they require. For brands aiming to grow efficiently while keeping quality intact, Reno provides a practical alternative to the higher costs and logistical challenges of the Bay Area.
What tax advantages does Nevada offer for businesses handling fragile electronics compared to California?
Nevada offers appealing tax advantages for businesses handling delicate electronics. One standout benefit is the absence of corporate and personal income taxes, a stark contrast to California. This can lead to significant savings in operating expenses.
On top of that, Nevada’s sales tax rates are generally lower. For instance, in Clark County, the rate is 8.375%, which is often more favorable compared to many areas in California. Another key perk? Nevada doesn’t impose taxes on digital products, whereas California includes many digital goods in its taxable categories. These tax policies position Nevada as a more budget-friendly and business-friendly choice for companies in this sector.
How does infrastructure impact the choice between fulfilling orders in the Bay Area or Reno?
When it comes to order fulfillment, infrastructure is a major deciding factor between the Bay Area and Reno. Reno stands out for its prime location, offering lower operating costs and quicker shipping times thanks to its proximity to key distribution routes. For businesses aiming to streamline shipping and save on expenses, this can be a game-changer.
Meanwhile, the Bay Area offers a more advanced infrastructure, featuring sophisticated logistics networks and access to a larger workforce. However, these benefits are often paired with higher expenses and the risk of delays caused by congestion. The ideal choice boils down to your brand's priorities - whether that's keeping costs low, speeding up delivery, or planning for growth.
Related posts
- Why Bay Area Logistics Matter for Fast-Growing eCommerce Brands
- Scalable eCommerce Fulfillment in California: What High-Volume DTC Brands Need to Know
- Bay Area Fulfillment for Fragile Electronics: A Guide for High-Tech Retailers
- Inside a Fulfillment Center for Electronics in Reno: Speed, Safety & Scale
Related Articles

How 3PLs Support Green Reverse Logistics
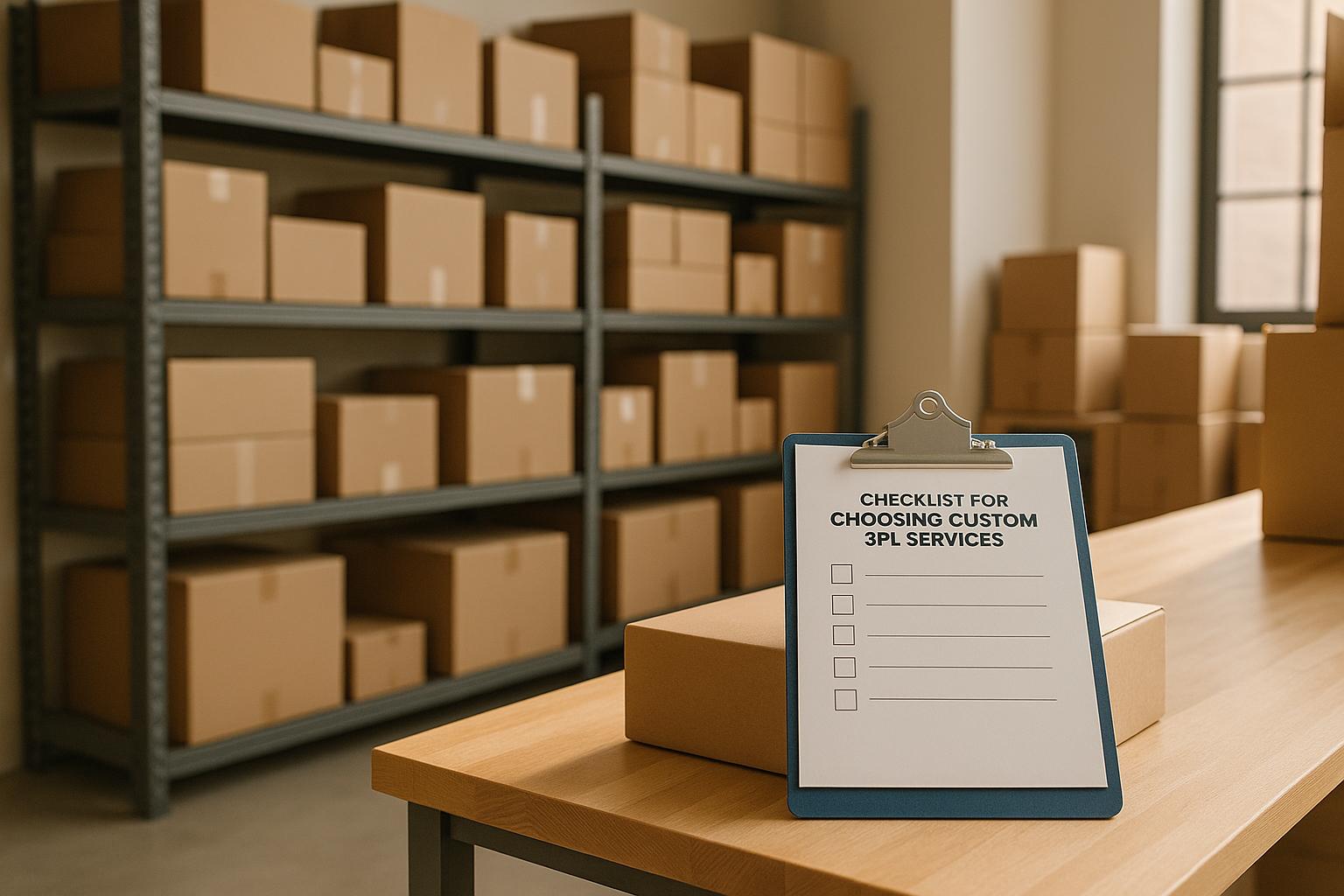
Checklist for Choosing Custom 3PL Services
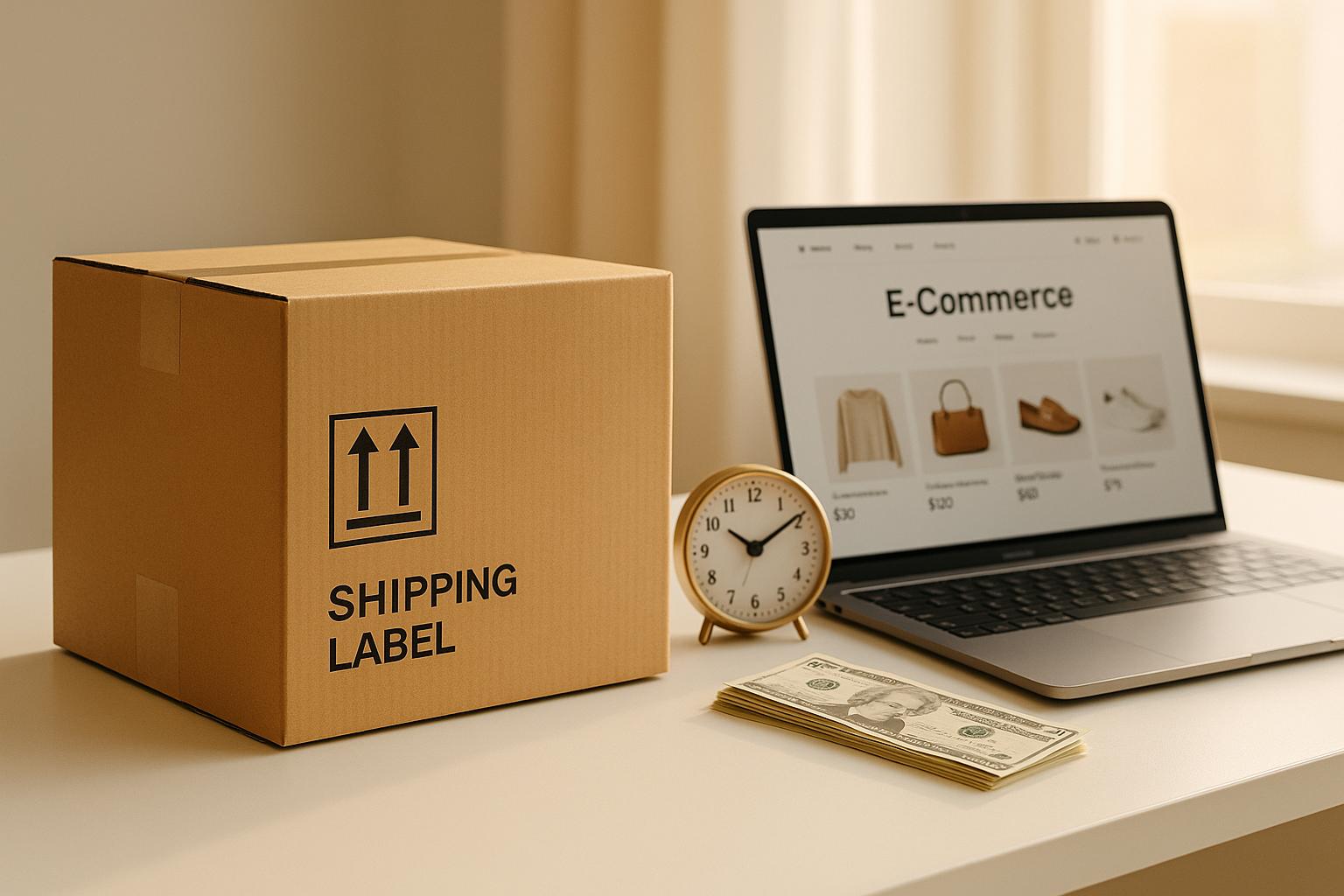