White Glove Services for Fragile Goods

White glove services offer a specialized solution for transporting fragile or high-value items with care and precision. These services go beyond standard shipping by providing tailored packaging, secure transportation, and on-site delivery support, minimizing risks like damage or mishandling. Industries like healthcare, technology, e-commerce, art, and pharmaceuticals rely heavily on these services to ensure their goods arrive safely and in perfect condition.
Key Highlights:
- Custom Packaging: Designed to protect fragile items using premium materials and techniques like double-boxing and foam inserts.
- Safe Transportation: Specialized vehicles with climate control and trained professionals reduce risks during transit.
- On-Site Support: Includes inside delivery, assembly, installation, and debris removal for a seamless experience.
- Industry Applications: Used for medical equipment, electronics, luxury goods, artwork, and temperature-sensitive items.
White glove services are essential for businesses aiming to safeguard delicate products while enhancing customer satisfaction. With growing demand, these services continue to set a high standard for premium logistics.
Beyond Delivery: White Glove Services for Critical Equipment
Key Components of White Glove Handling
White glove handling revolves around three main pillars, each working together to safeguard delicate items throughout their journey. These components ensure goods arrive intact and ready for use.
Custom Packaging and Crating
The first step in white glove services is creating tailored packaging solutions that cater to the specific needs of each item. Unlike generic shipping boxes, custom packaging uses premium materials designed to shield fragile goods from damage.
This often includes bubble wrap, foam inserts, corrugated cardboard, and custom enclosures. Techniques like double-boxing and clearly marked "Fragile" labels add extra layers of protection. Proper labeling, such as "Handle with Care", ensures everyone involved in the process knows to treat the items delicately.
Sustainability is becoming a priority in packaging, given that the industry produces over 2 million tons of waste annually. In 2024, Cruz Foam introduced recyclable and compostable packaging options, including specialized solutions for items like glassware and pharmaceuticals. These innovations not only protect goods but also reduce environmental impact.
Strong, custom packaging lays the groundwork for secure transport, where expert handling takes over to protect fragile items.
Safe Handling and Transportation
The transportation phase is often the riskiest for fragile goods, making specialized vehicles and equipment essential. Vehicles equipped with air-ride suspensions reduce vibrations, while climate-controlled options maintain consistent temperature and humidity levels - critical for sensitive items.
Skilled professionals play a key role here. They undergo extensive training to master proper lifting techniques, equipment use, and handling protocols tailored to different types of fragile goods. From carefully loading items to securing them with specialized restraints, every step is designed to minimize risk.
Real-time GPS tracking and monitoring add another layer of security, enabling immediate action if issues arise during transit. For instance, in August 2024, Aria Logistics successfully transported a large, delicate sculpture to a museum exhibition. They used a custom crate with shock-absorbing materials and climate-controlled trucks to ensure the piece arrived in pristine condition, ready for display.
On-Site Services and Support
The final stage of white glove handling focuses on precise delivery and professional setup. Inside delivery ensures items are brought directly to their intended location within a building, eliminating the risks of customer mishandling. Teams expertly navigate tight spaces, stairs, and elevators while maintaining full control over fragile goods.
Unpacking and assembly services take the hassle out of setup. Trained technicians follow manufacturer guidelines to assemble items correctly, reducing the chance of damage during installation. For complex items, installation services include positioning, system connections, and functionality checks to ensure everything works as intended before the team leaves.
Debris removal is another valuable feature, clearing away packaging materials and leaving the space clean and ready for use. The demand for such comprehensive services is growing, with the global white glove market projected to reach $8.2 billion by 2028. This rise is partly driven by the increasing need for careful handling of high-value items like computers and consumer electronics, which account for 22% of all e-commerce sales.
At JIT Transportation, these three components - custom packaging, safe transportation, and on-site support - form the foundation of our white glove services, ensuring every item is handled with care from start to finish.
Step-by-Step Guide to Packaging, Transportation, and Delivery
White glove logistics follows a detailed process, ensuring every step from assessment to delivery is handled with precision.
Assessing Item Fragility and Requirements
Every successful white glove delivery starts with a close evaluation of the item's characteristics and vulnerabilities. This step is crucial to determine the level of protection and specific handling needed throughout the journey.
"Recognizing the specific needs of each type of fragile item is vital in determining the most suitable packing materials and handling procedures." – Cowtown Logistics Freight Management
Understanding the unique challenges of different materials is key. For instance, glass can shatter easily, while electronics may be prone to damage from static or moisture. By documenting details such as size, weight distribution, and weak points, you can create a shipping plan tailored to the item's needs.
Environmental factors also play a role. Temperature changes, humidity, vibrations, or the need for specific orientations (e.g., keeping an item upright) must be accounted for. Clear labels indicating special handling requirements are essential to prevent accidents.
Failing to assess properly can have serious repercussions. In one case from 2014, improperly labeled hazardous chemicals leaked during transit, leading to evacuations and costly cleanup efforts. Similarly, fragile electronics have been damaged due to insufficient packaging and unclear instructions, emphasizing the importance of careful planning.
Once vulnerabilities are identified, the next step is implementing customized protective measures.
Protective Packaging and Secure Loading
Using the right materials and methods for packaging is critical to safeguarding items during transit. High-quality, double-walled boxes are a great starting point, and fragile items should be individually wrapped with bubble wrap or foam sheets. Studies show that advanced shock-absorbing materials can cut breakage rates for glassware by 25%.
To further reduce risks, fill empty spaces in boxes with packing peanuts, air pillows, or crumpled paper. Properly balance the load by placing heavier items at the bottom and lighter ones on top. Dividers and extra cushioning help prevent items from shifting and colliding. This is particularly important given that physical impacts during transit account for around 25% of cargo damage.
Handling fragile items also requires the right equipment. Tools like forklifts, pallet jacks, and hoists can help avoid stacking or overloading, which might compromise the packaging and increase breakage risks.
Stability during transit is just as important. Use anti-tip straps or elastic netting to keep shipments secure inside the vehicle. Thoroughly seal boxes with packing tape along all seams, and clearly label them with "Fragile" and "This Side Up" instructions. Since over half of customers report receiving damaged goods due to poor packaging, these details are critical for maintaining trust and satisfaction.
Planning and Executing White Glove Delivery
Once items are assessed and securely packaged, the focus shifts to planning the delivery with precision.
Route optimization is key. Consider factors like transport type, packaging needs, and environmental conditions to minimize transit time and reduce the chance of damage. Real-time tracking tools provide visibility into the delivery process, allowing for quick adjustments if unexpected issues arise. Partnering with a third-party logistics provider (3PL) that uses advanced technology can further enhance tracking and performance monitoring.
Equally important is ensuring that delivery personnel are well-trained in handling premium services. Clear communication with customers about delivery timeframes, setup procedures, and special requirements ensures smooth execution.
At the final destination, white glove delivery involves more than just dropping off the package. It includes careful inspection, precise placement of items, and proper disposal of packaging materials. These steps are directly tied to the initial assessment and packaging, ensuring every detail is addressed. Tailoring the delivery process to meet specific customer needs, including scheduling and placement instructions, reinforces the high standard of care established earlier.
At JIT Transportation, we take pride in our methodical approach to packaging, transportation, and delivery. By combining advanced technology with hands-on expertise, our team guarantees that every fragile shipment gets the specialized care it deserves.
sbb-itb-eafa320
Value-Added Services and Customer Experience
White glove logistics goes beyond standard delivery. It offers additional services that not only safeguard fragile goods but also elevate the customer experience. Let’s dive into the range of services that make this possible.
Range of Value-Added Services
These services include asset tagging for accurate inventory tracking, detailed inspections to ensure quality, and product testing to verify functionality - especially critical for delicate or sensitive equipment.
Flexible delivery scheduling is another key feature, allowing deliveries during specific time slots or even outside normal business hours. This flexibility is invaluable for businesses that need to avoid operational downtime or for residential customers with limited availability.
Additionally, customized packaging protocols address the unique vulnerabilities of each item, using specialized materials and techniques that go far beyond standard shipping practices.
For example, in August 2023, Crane Worldwide Logistics showcased the impact of these services by assisting a Fortune 100 technology company with the global transport of integrated data server racks. The company had faced persistent issues like shipment errors, product damage, and unreliable delivery schedules. By implementing specialized handling, advanced tracking, and coordinated logistics, Crane Worldwide ensured the safe and timely transport of the client’s high-value equipment.
These services not only enhance protection but also pave the way for smooth and transparent communication throughout the shipping process.
Real-Time Communication and Transparency
Modern white glove logistics relies on advanced technology to provide unparalleled visibility. Real-time tracking keeps customers updated at every step, from departure to delivery, fostering trust and transparency. Proactive updates alert customers to any delays, reinforcing confidence in the process.
Data-driven tracking tools significantly reduce delays. Technologies like GPS, RFID tags, and IoT devices allow logistics teams to quickly identify and address potential issues while keeping customers informed.
"In today's fast-paced supply chain, real-time tracking is not a luxury – it is a competitive advantage." - Giuseppe Pavesi, Senior Manager Products and Solutions at DB SCHENKER
This level of transparency not only minimizes uncertainties but also contributes to a better overall customer experience.
Improving Customer Satisfaction
Comprehensive services and transparent communication come together to create a personalized delivery experience. For instance, assembly and installation services ensure that fragile items are not just delivered safely but are also set up and ready for immediate use. This reduces the risk of damage during unpacking and adds instant value for customers.
The demand for such premium services is on the rise. The white glove delivery market is projected to grow from $75.56 billion in 2024 to $104.63 billion by 2029, with an annual growth rate of 6.85%. Careful handling and professional setup leave a lasting impression, building customer loyalty and encouraging repeat business. When items arrive intact, properly installed, and ready for use, customers associate that positive experience with the brand itself.
Damage-free deliveries also translate to cost savings by reducing returns, replacements, and customer service issues. Investing in white glove services often proves worthwhile through higher customer satisfaction and retention.
At JIT Transportation, we take pride in offering personalized delivery and expert installation, ensuring every item is ready for use upon arrival. Our value-added services go beyond transportation, covering solutions like pick & pack, kitting & assembly, testing, and specialized handling. With our advanced technology platform providing real-time updates and a dedicated team focused on precision, we ensure every customer interaction reflects our commitment to excellence.
Best Practices and Compliance in White Glove Services
Delivering outstanding white glove services goes beyond simply handling items with care. It requires a well-trained team, adherence to strict regulations, and a commitment to refining processes over time.
Staff Training and Expertise
The backbone of any successful white glove service is a team of skilled professionals. These individuals must be trained not only in technical handling but also in providing exceptional customer experiences. Training programs should focus on key areas like proper lifting techniques, secure packaging, and careful loading to minimize the risk of damage. Regular training updates ensure that staff stay aligned with the latest industry methods.
Certain industries demand even more specialized knowledge. For instance, professionals in art logistics receive specific training for tasks like packing delicate paintings and working alongside art handlers to install pieces in clients' homes.
Adhering to Industry Standards
In addition to skilled personnel, strict compliance with industry standards is essential. White glove service providers must navigate a range of regulations, including shipping protocols, customs requirements, safety measures, and environmental guidelines. This includes mastering customs clearance processes, understanding HS codes, and accurately classifying tariffs.
Sustainability also plays a key role in compliance. Practices like using reusable packaging, optimizing delivery routes, and choosing energy-efficient transportation methods not only meet regulatory demands but can also reduce operational costs. Advanced tracking technologies further support compliance by providing real-time shipment visibility and detailed reporting.
Continuous Evaluation and Improvement
Excellence in white glove services isn't a one-time achievement - it’s an ongoing effort. Regular evaluations and audits are critical for identifying areas of improvement. Feedback from both employees and customers can uncover inefficiencies and inspire updates to packaging methods, delivery processes, and overall service quality.
At JIT Transportation, these principles are at the heart of our operations. Our team undergoes extensive training in specialized handling techniques and maintains strict adherence to industry regulations. By incorporating regular process reviews and listening to customer feedback, we continually enhance our white glove services to ensure the highest levels of care and professionalism.
Conclusion
White glove services have become a game-changer for businesses that deal with fragile or high-value products. By focusing on specialized care, tailored packaging, and careful handling, these services significantly lower the chances of damage while elevating customer satisfaction. Whether it's shipping delicate artwork or sensitive electronics, white glove logistics ensures items reach their destination in perfect condition.
The demand for these premium logistics solutions continues to grow.
"White glove logistics is one of the biggest ways businesses can exceed customer expectations and drive business success." - AFP Global Logistics
Choosing white glove services can lead to measurable benefits, including fewer damage claims, better security, and stronger customer loyalty. These services go beyond standard shipping by offering features like custom packaging, climate-controlled transport, real-time tracking, and even value-added options such as assembly and installation - catering to the specific needs of every shipment.
For fragile or specialized deliveries, white glove services are more than just an option - they’re a smart investment. At JIT Transportation, we’re committed to ensuring every item is handled with expert care from start to finish, protecting both your products and your reputation.
FAQs
What are the advantages of using white glove services for shipping fragile goods?
White glove services provide dedicated care for delicate or fragile items, ensuring they are managed with the utmost attention and skill. These services go beyond standard shipping, offering secure packaging, cautious transportation, and careful delivery to reduce the chances of damage while giving you peace of mind.
What sets white glove delivery apart is the added conveniences it offers. This can include unpacking, assembling, and placing items exactly where they need to go. It's especially suited for goods that require careful handling or a specific setup. This tailored service not only protects your items but also enhances the overall customer experience, ensuring everything arrives in pristine condition.
How do white glove services protect temperature-sensitive items during transportation?
White glove services are designed to protect temperature-sensitive items by using climate-controlled vehicles. These vehicles maintain a steady temperature, shielding shipments from damage caused by extreme heat or cold. They’re specifically built to handle delicate goods like medical supplies or fragile items that demand precise conditions.
Beyond the vehicles, these services follow strict handling protocols. Items are carefully packed, monitored throughout the journey, and transported with exceptional care. Every stage of the process is meticulously planned to ensure sensitive products stay intact and reach their destination in flawless condition.
How do white glove services ensure sustainable packaging and transportation practices?
White glove services are stepping up their game by focusing on eco-conscious practices. They're swapping out traditional materials for biodegradable, recyclable, and reusable packaging, cutting down on waste and aiming for a smaller environmental footprint. To make things even better, many providers are rethinking their packaging designs to use less material without compromising strength - balancing efficiency with practicality.
Some companies are also experimenting with plant-based and compostable packaging, pushing the boundaries of what's possible in sustainable logistics. These steps not only support a more environmentally friendly supply chain but also uphold the meticulous care and quality that white glove services are known for.
Related posts
Related Articles
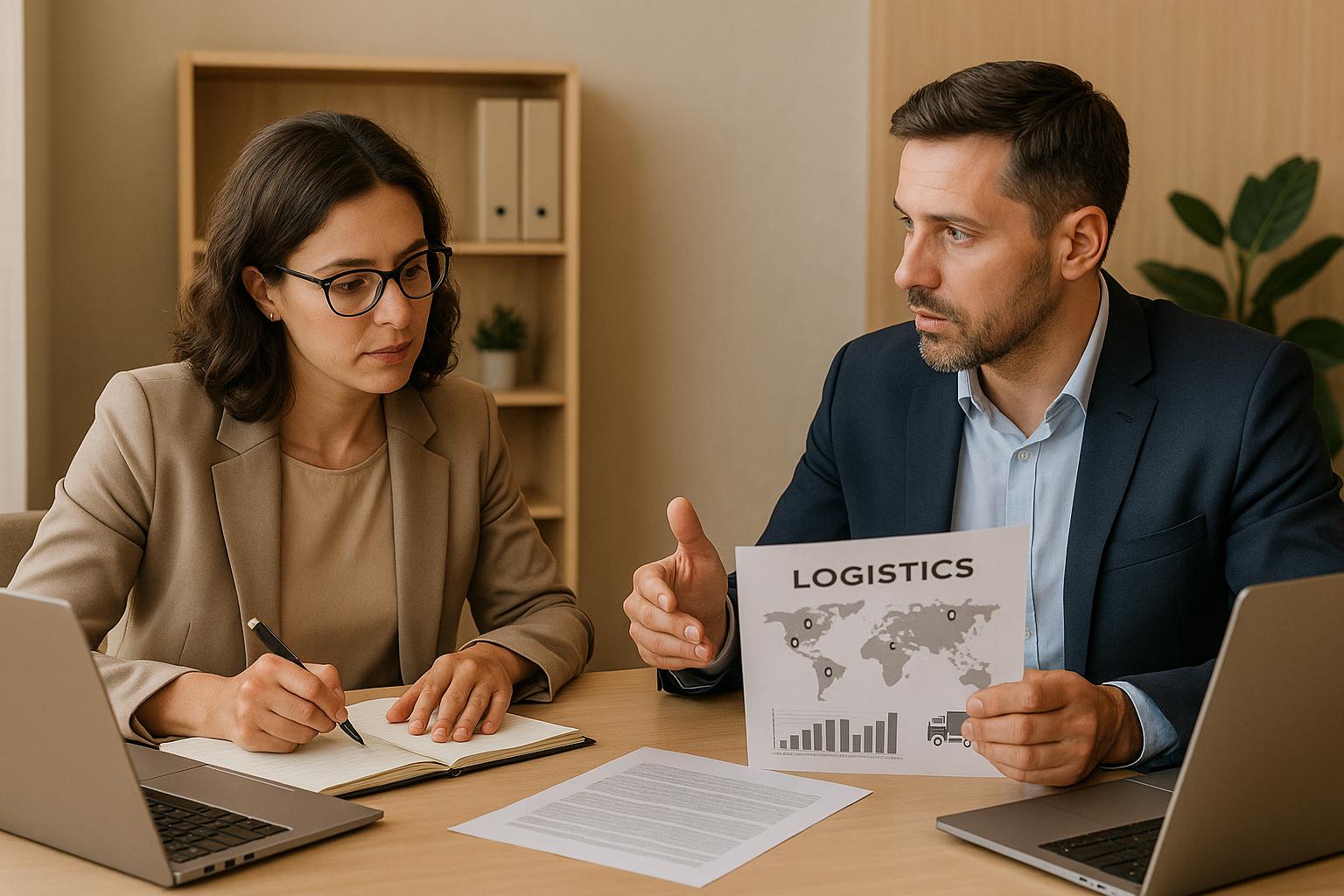
Questions to Ask Before Partnering with a 3PL

How 3PLs Support Green Reverse Logistics
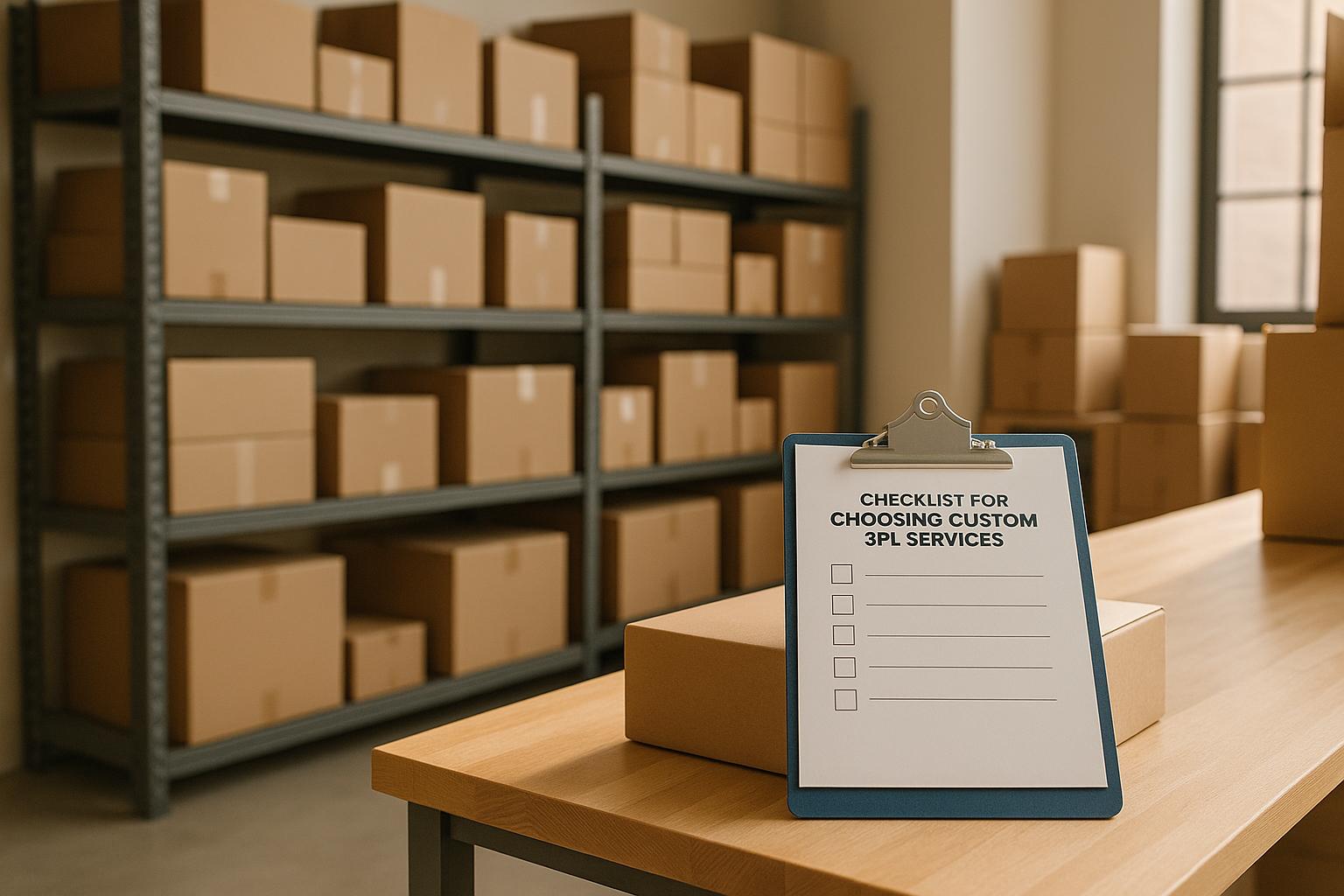